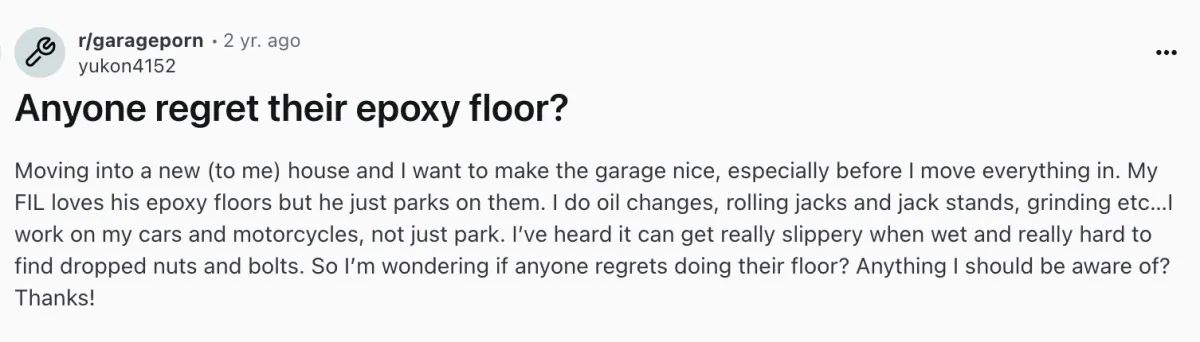
How Much Does Epoxy Flooring Cost?
How Much Does Epoxy Flooring Cost In Miami / Fort Lauderdale?
National Average Cost: $7.50/sq. ft.
All cost data throughout this article was collected from Today's Homeowner.
Epoxy flooring can be the perfect modernizing solution for drab, dull concrete floors. On average, they cost between $3 and $12 per square foot, which is cheaper than many flooring replacement alternatives. If you’re searching for a long-lasting and beautiful flooring option, epoxy garage floors might be your best bet. This guide reviews the specifics surrounding the cost of installing epoxy floors.
Comparing Flooring Alternatives: Hardwood, Carpet, and Laminate
When considering flooring options, it’s essential to weigh the costs, durability, and design elements of each. While epoxy flooring is a versatile and cost-effective solution, let’s explore how it stacks up against other popular choices like hardwood, carpet, and laminate.
Hardwood Flooring
Hardwood floors offer a timeless, polished aesthetic but come with a higher price point. On average, the sale price for hardwood ranges between $8 and $15 per square foot for materials, not including installation. If moisture or wear and tear is a concern, consider waterproofing or applying a protective primer to maintain the longevity of your investment.
Carpeted Flooring
Carpeting is a warm and cushioned option, costing between $3 and $10 per square foot depending on the design, material, and thickness. However, carpeted flooring requires frequent cleaning, particularly in humid climates like Miami, to prevent issues like mold or trapped moisture. For high-traffic areas, epoxy flooring is often a better choice due to its superior resistance to wear.
Laminate Flooring
Laminate floors are an affordable option, costing between $1 and $6 per square foot, depending on the thickness of the fiberboard base layer. While laminate flooring mimics the look of natural wood or stone, it’s less resistant to abrasion, water damage, and heavy impacts compared to epoxy floors or polished concrete.
What Are Factors in Calculating the Cost of Epoxy Floor Coating?
Every epoxy flooring installation is unique, and costs can vary significantly from one home to another. Several factors influence the sale price, including the application method, labor costs, required materials and equipment, the size of the room, necessary site preparation, and the type of epoxy chosen.
The table below provides a quick overview of pricing based on key variables. For a deeper dive into how factors like moisture, primer, and resin choice affect the cost, continue reading beyond the chart.
Local Regulations:
In Miami and Fort Lauderdale, epoxy flooring installations must adhere to the Florida Building Code, which sets standards for construction practices to ensure safety and durability. As of January 1, 2024, the City of Fort Lauderdale requires all permit applications and plans to be submitted digitally via the LauderBuild Plan Room. It's essential to consult with local building authorities or a licensed contractor to determine if your specific epoxy flooring project necessitates a permit. Compliance with local regulations ensures that your installation meets all safety and quality standards.
City of Fort Lauderdale, FL | Home
Maintenance Advice:
Maintaining epoxy floors in humid climates like South Florida requires particular attention to prevent moisture-related issues. Here are some tips:
Climate Considerations: Epoxy floors are well-suited for hot and humid climates due to their resistance to moisture penetration, which helps prevent mold and mildew growth. Apex
Cleaning Practices: Regularly sweep and mop the floor to remove dirt and debris. Avoid using stiff-bristle brushes or caustic cleaning solutions, as they can damage the epoxy surface. Carboline
Humidity Control: During installation, it's crucial to maintain appropriate humidity levels, as high humidity can affect the curing process of epoxy coatings. Once cured, epoxy floors are highly resilient to humidity. Epoxy Colorado
Environmental Considerations:
For those concerned about indoor air quality and environmental impact, opting for low-VOC (Volatile Organic Compounds) epoxy products is advisable. These eco-friendly options emit fewer harmful chemicals during application and curing, making them safer for both installers and occupants. Additionally, choosing water-based epoxies can further reduce environmental impact, as they typically contain lower levels of VOCs compared to solvent-based alternatives.
By adhering to local regulations, implementing proper maintenance practices, and considering environmentally friendly products, you can ensure that your epoxy flooring is durable, safe, and sustainable in the Miami and Fort Lauderdale climate.
Type of Epoxy
When choosing epoxy flooring for your home, it’s important to select the right type based on your budget, durability needs, and the desired aesthetic. The three main types are water-based epoxy, solvent-based epoxy, and pure solid epoxy. Each option offers unique benefits and varying levels of adhesion, wear resistance, and cost.
Pure Solid Epoxy: As the most durable and long-lasting option, solid epoxy flooring is made of 100% resin and hardening agents. Its superior resistance to abrasion, corrosion, and heavy equipment makes it ideal for warehouses, garage floors, and industrial applications. However, this durability comes at a higher price, as it’s the most expensive option and usually requires professional installation.
Solvent-Based Epoxy: A middle-tier choice, solvent-based epoxy offers better adhesion and strength than water-based epoxy but is not as robust as pure solid epoxy. Its glossy finish enhances the aesthetics of the floor, but due to its high VOC (volatile organic compound) content, it’s less environmentally friendly. Additionally, some states may restrict its use due to chemistry regulations.
Water-Based Epoxy: If you’re looking for a budget-friendly option, water-based epoxy is a practical choice. It’s easy to work with, low in VOC emissions, and safe for indoor spaces, making it more environmentally friendly than solvent-based alternatives. While it’s less durable and susceptible to wear and tear, it’s great for home improvement projects in low-traffic areas or spaces like countertops or residential garages.
The cost of your epoxy flooring installation will vary depending on the type of epoxy you choose. Most homeowners pay between $0.50 and $3 per square foot for materials, with additional costs for primer, pigments, or decorative enhancements like quartz flakes.
Application Method
The application method for your epoxy flooring installation can significantly impact the overall cost and final result. The best method depends on the type of epoxy you select, the complexity of the design, and whether you choose to hire a professional or tackle the project as a DIY.
Water-Based Epoxy Application: Water-based epoxy is relatively straightforward to install, making it an excellent option for DIY enthusiasts or budget-conscious homeowners. This method doesn’t typically require specialized tools and keeps labor costs low. However, while it’s easy to apply, it lacks the durability of solid epoxy, making it more suited for light-use areas like countertops or pedestrian traffic spaces.
Solid Epoxy Application: Installing solid epoxy flooring is far more complex and usually requires professional expertise due to its low pot life (the time it remains workable after being mixed) and the need for precise techniques. Professionals use specialized tools such as spiked rollers, trowels, and floor scrubbers to ensure even adhesion and a seamless finish. This process is ideal for garages, warehouses, or areas exposed to heavy wear and tear. Expect higher costs for both labor and materials when opting for solid epoxy, but the result is unmatched durability and abrasion resistance.
Decorative Epoxy Applications: Adding decorative elements like metallic finishes, quartz flakes, or custom colors elevates the aesthetic appeal of your floors but also increases the cost. These designs require advanced techniques and careful layering, which can add $5 to $12 per square foot to the total price. Such custom features are ideal for renovations aiming to blend design with functionality, whether in a garage, warehouse, or residential setting.
Regardless of the method, proper primer application and substrate preparation are critical for ensuring long-lasting adhesion and resistance to moisture, corrosion, and daily wear. Consulting with a professional contractor can help determine the best application technique for your specific needs and ensure your investment lasts for years.
Labor Costs
If you’re not taking the DIY route, labor costs will form a significant part of your epoxy flooring installation expenses. In fact, labor can account for up to 65% of the total price, making it a crucial factor in your project budget.
Average Labor Costs: Most professional contractors charge between $4 and $7 per square foot for epoxy flooring installations, depending on the scope of the job, the type of epoxy, and local market rates. Alternatively, if the contractor charges hourly, expect rates between $50 and $150 per hour, especially for more intricate installations like metallic epoxy or floors with decorative quartz flakes.
Overhead and Additional Fees: Beyond standard labor rates, contractors may include a flat fee to cover overhead expenses. This fee often encompasses tools, travel, and specialized materials required for the installation, such as spiked rollers, primer, or protective equipment. These costs will vary depending on the contractor and the complexity of the project.
Warranty Options: Most reputable contractors offer a warranty on their work, ensuring your investment is protected from defects or poor workmanship. When hiring a professional, inquire about the specifics of their warranty to ensure your resin floors are built to last under daily wear and tear.
Hiring a professional not only ensures high-quality results but also saves time and reduces the risks associated with improper adhesion or moisture issues. For larger projects like warehouse floors or garage renovations, the expertise of a contractor often justifies the higher costs.
Materials and Equipment for Epoxy Flooring Installation
Installing an epoxy floor system requires a range of specialized tools and materials to achieve a durable, seamless finish. Whether you’re tackling this as a DIY project or hiring a professional contractor, the proper equipment is essential for ensuring adhesion, even application, and long-lasting results.
Essential Tools and Materials
To complete an epoxy flooring project, you’ll typically need:
Spiked Rollers – Used to remove air bubbles and evenly distribute the epoxy.
Wet-Dry Vacuums – Essential for cleaning debris and ensuring the surface is free of dust before application.
Power Washers – Used for surface preparation, particularly on outdoor or heavily soiled concrete.
Squeegees – For spreading the epoxy evenly across the surface.
Sprayers – For applying sealants, primers, or decorative elements like pigments or color enhancers.
Protective Equipment – Including gloves, goggles, and respirators to protect against chemistry hazards like VOCs.
Specialized Shoes – Spiked shoes are worn to walk over wet epoxy without leaving footprints, ensuring consistency in the finish.
DIY Costs vs. Contractor Fees
If you’re taking the DIY route, you’ll need to purchase these tools unless you already own them. Many hardware stores or online retailers offer epoxy floor kits that include the necessary equipment and materials for smaller projects. However, for larger or more complex installations, you may need to buy additional items, such as industrial-grade floor scrubbers or filler materials for repairing cracks.
For those hiring a professional, the cost of tools and materials is typically included in the contractor’s estimate. Contractors factor these expenses into their pricing, covering items like spiked rollers, sprayers, and other specialized equipment. While this adds to the overall sale price, it eliminates the need for you to source materials and ensures a professional-quality result.
Pro Tip:
Proper equipment is crucial to avoid inconsistencies in the application process. Inadequate preparation or missing tools can lead to poor adhesion, moisture issues, or uneven wear, significantly reducing the lifespan of your epoxy flooring.
Room Size and Its Impact on Epoxy Flooring Costs
The size of your project plays a major role in determining the total cost of your epoxy flooring installation. Larger spaces require more materials, time, and labor, which naturally increases the sale price. Whether you’re hiring a contractor or taking the DIY route, bigger jobs generally cost more due to the additional resin, primers, and other materials needed.
Cost Examples by Room Size
Three-Car Garage (700 sq. ft.): Costs for a larger garage range from $2,200 to $9,500, depending on the type of epoxy and whether any customizations (like metallic finishes or decorative quartz flakes) are added.
One-Car Garage (200 sq. ft.): A smaller one-car garage can cost between $700 and $2,900, making it a budget-friendly option for homeowners looking to modernize their space with durable epoxy flooring.
Basement (1,000 sq. ft.): Typical costs for a basement range from $2,800 to $11,500, with price fluctuations depending on the design, application method, and the level of site preparation required.
Material Choice Matters
While larger spaces tend to cost more overall, your choice of epoxy can significantly affect the final cost. For example, opting for water-based epoxy, which is more affordable, could result in a large installation costing the same as a smaller space that uses premium solid epoxy. Customization features like pigments, traffic coatings, or colored resin will also drive up the price.
Pro Tip:
If you’re working on a tight budget, consider focusing on durable epoxy options for high-traffic areas like garages or warehouses, while using less expensive alternatives in lower-use spaces. Be sure to factor in additional costs for moisture control, site preparation, or primer application, which are crucial for achieving long-lasting results.
Site Preparation for Epoxy Flooring
Proper site preparation is essential for a successful epoxy flooring installation. Without adequate preparation, the epoxy may fail to adhere correctly, leading to a finish that is prone to moisture issues, wear, and adhesion problems. Completing the necessary prep work ensures a smooth, durable, and visually appealing surface.
Common Site Preparation Techniques
The amount and type of preparation required depend on the condition of your existing flooring. Here are some common methods:
Power Washing: Removes dirt, oil, and debris, ensuring the surface is clean and ready for the epoxy application.
Acid Etching: A chemical process that roughens the concrete for better adhesion. DIYers can purchase acid etching chemicals for approximately $20 per bottle.
Sandblasting: An effective technique for removing old coatings or tough stains while creating a rough texture for the epoxy. Sandblasting typically costs between $1 and $5 per square foot.
DIY vs. Professional Preparation
If you’re tackling the project yourself, you’ll need to purchase or rent the necessary tools, including power washers, acid etching kits, or sandblasting equipment. This additional expense should be factored into your overall sale price if you opt for a DIY approach.
For those hiring a contractor, the costs of site preparation are usually included in the contractor’s estimate. Professional contractors typically have access to industrial-grade tools and the expertise required to handle uneven surfaces, cracks, or crumbling concrete slabs. This ensures better results and saves time compared to DIY efforts.
Pro Tip:
Floors with significant damage, such as large cracks or deteriorated cement, may require additional prep work like resurfacing or filler application before epoxy can be applied. These steps are essential for achieving long-lasting adhesion and preventing premature wear and tear.
What Are Additional Cost Considerations When Installing Epoxy Flooring?
Several other factors can also influence the overall price of your epoxy flooring.
Repairing Concrete Before Epoxy Installation
While concrete slabs are known for their durability, they can develop wear and tear over time, especially after several decades. Issues like cracks or chips may result from poor workmanship or natural deterioration. Regardless of the cause, addressing these problems is critical to ensure the epoxy coating adheres properly and creates a long-lasting finish.
Repair Costs for Minor Damage: Small cracks and chips can typically be repaired by professionals at a cost of $6 to $14 per square foot. These repairs are essential for creating a smooth surface and avoiding issues with adhesion or moisture penetration once the epoxy is applied.
Major Foundation Repairs: If the concrete foundation shows signs of severe damage, such as crumbling or large cracks, it could indicate structural failure. In such cases, it’s essential to hire an inspector to assess the damage and recommend the best course of action. Repairing a failing foundation can range between $2,200 and $7,800, depending on the extent of the damage and the required work.
Pro Tip:
Investing in concrete repairs before applying an epoxy coating will significantly extend the lifespan of your flooring system by preventing premature wear and tear, moisture issues, and uneven surfaces.
Resurfacing Concrete for Epoxy Flooring
In certain cases, resurfacing the concrete substrate is necessary before installing an epoxy flooring system. This process addresses a variety of issues, such as uneven surfaces, minor damage, or worn-out areas, and provides a smooth base for optimal adhesion of the epoxy coating. Resurfacing is often a more cost-effective and less labor-intensive solution than tearing out and replacing the existing concrete entirely.
Cost of Resurfacing: The price for resurfacing concrete typically ranges from $3 to $25 per square foot, depending on factors such as:
The extent of the damage being repaired
The tools and materials required
Whether decorative elements like polished finishes or pigments are included
This wide price range reflects the variations in project size, complexity, and any additional customizations.
Pro Tip:
Resurfacing is ideal for addressing cosmetic or surface-level issues. However, if your concrete slab has significant structural damage, you may need more extensive repairs before applying epoxy. Proper resurfacing ensures long-lasting durability and prevents future wear and tear under heavy use.
Painting and Sealing Concrete After Epoxy Installation
Once the epoxy flooring is installed, some homeowners choose to enhance the finish by adding a top coat of sealant or paint. These final touches not only improve the floor’s durability but also allow for greater customization, helping the flooring blend seamlessly with the surrounding design.
Costs for Painting and Sealing
Labor Costs: If you hire a contractor, expect to pay between $40 and $150 per hour for the additional labor involved in applying the sealant or paint.
Square Footage Rates: Some contractors charge based on the size of the project, with costs ranging from $1.50 to $5 per square foot.
Why Add a Sealant or Paint?
Increased Durability: A top coat of polyurethane or traffic-grade sealer can further protect the floor from abrasion, wear, and exposure to chemicals or heavy equipment.
Aesthetic Customization: Adding pigments, colored sealants, or even a polished finish can create a high-end look tailored to your preferences.
Moisture Protection: Sealing can provide an extra layer of defense against moisture, ensuring long-lasting adhesion and protecting the underlying concrete slab.
Pro Tip:
Adding a sealant or paint after epoxy installation is especially beneficial for high-traffic areas like garages, driveways, or warehouses, where corrosion and wear and tear are more likely.
Traffic Coating for Enhanced Durability
While a standard sealant may be sufficient for some epoxy flooring installations, high-traffic areas often require additional protection. In these cases, traffic coatings are the ideal solution. These industrial-grade coatings provide superior abrasion resistance and durability, making them perfect for spaces exposed to heavy foot traffic or vehicle traffic.
Benefits of Traffic Coatings
Enhanced Durability: Designed to withstand wear and tear from frequent use, traffic coatings protect the flooring in high-traffic areas such as warehouses, garages, or homes with large families.
Heavy Equipment Compatibility: Ideal for spaces with heavy equipment or machinery, traffic coatings reduce the risk of damage to both the flooring and the tools.
Longer Lifespan: By adding an extra layer of protection, traffic coatings significantly extend the life of your epoxy flooring, minimizing the need for repairs or replacements.
Cost of Traffic Coatings
Expect to pay 20% to 30% more than the price of standard sealers when opting for traffic coatings. The added expense is a worthwhile investment for those seeking enhanced durability in high-use environments.
Pro Tip:
Traffic coatings are especially valuable for driveways, warehouses, and commercial epoxy flooring projects, where abrasion resistance, moisture control, and corrosion protection are critical.
What Is Epoxy Flooring?
Epoxy flooring, also known as resinous flooring, is a type of synthetic resin coating applied over concrete substrates to create a durable and visually appealing surface. Commonly used in garages and basements, this robust material is gaining popularity in various parts of the home, including patios, kitchens, and bathrooms, due to its unique combination of functionality and style.
How It Works
Unlike traditional flooring, which requires precise cuts and careful measurements, epoxy flooring starts as a liquid that is poured over the concrete slab. Once the resin cures, it forms a solid, seamless surface that is:
Extremely Durable – Resistant to abrasion, wear and tear, and daily use in high-traffic areas.
Moisture-Resistant – Ideal for humid climates or areas prone to spills.
Chemical Resistant – Can withstand exposure to oil, grease, and chemical spills without damage.
Where Is Epoxy Flooring Used?
While its durability makes it a popular choice for garages and shops, epoxy flooring is versatile enough for a range of spaces:
Basements: Provides a sleek, low-maintenance solution for below-ground spaces.
Kitchens and Bathrooms: Offers a modern, water-resistant option that stands up to heavy use.
Patios: Enhances outdoor living spaces with its weather-resistant properties.
Why Choose Epoxy Flooring?
Epoxy flooring combines design and functionality, making it an excellent choice for home improvement projects or renovations. Its resin base ensures a long-lasting finish that is as aesthetic as it is practical.
What Are the Different Types of Epoxy Flooring?
Choosing the right type of epoxy flooring is crucial for achieving the desired durability, finish, and functionality. There are three primary types of epoxy to consider: solid epoxy, solvent-based epoxy, and water-based epoxy. Each offers unique benefits and is suitable for different applications based on your budget, environmental considerations, and the specific demands of the space.
Solid Epoxy
Solid epoxy is the most durable and long-lasting option among epoxy types, making it a top choice for those with a flexible budget. Composed of 100% epoxy and hardening agents, it is highly resistant to oil, grease, water, chips, and scuffs, allowing it to withstand heavy traffic and abrasion with ease.
Key Benefits of Solid Epoxy
Industrial Strength: Ideal for commercial epoxy flooring, warehouses, and industrial settings, where durability is a top priority.
Environmentally Friendly: Unlike some alternatives, solid epoxy is free of volatile organic compounds (VOCs), making it a safer choice for indoor applications.
Exceptional Longevity: When installed properly, solid epoxy can last for decades, even in high-traffic areas, with minimal wear and tear.
Important Considerations
While solid epoxy delivers unparalleled durability, it has some drawbacks:
Professional Installation Required: Its low pot life—the time epoxy remains workable—demands rapid application using specialized tools and techniques, making professional installation essential.
Higher Costs: Solid epoxy is the priciest option, but its long lifespan can make it a cost-effective investment for spaces requiring maximum resilience.
Moisture Sensitivity: It isn’t suitable for floors with underlying moisture problems, as improper adhesion can lead to peeling or bubbling.
Best Applications for Solid Epoxy
This type of epoxy is perfect for garages, industrial settings, and manufacturing facilities where heavy equipment, frequent use, and abrasion resistance are critical.
Solvent-based Epoxy
Solvent-based epoxy is a versatile mid-tier option that combines epoxy resin with solvents to produce a sleek, glossy finish. Offering greater durability and longevity than water-based alternatives, this type of epoxy strikes a balance between affordability and performance.
Key Benefits of Solvent-Based Epoxy
Durability and Longevity: More robust than water-based epoxy, it performs well under moderate traffic and in residential or commercial settings.
Easy Application: This epoxy type is less affected by temperature changes and humidity, making it easier to install in varied conditions.
Quick Drying Time: It dries faster than other types, reducing wait times and enabling a more efficient installation process.
Important Considerations
While solvent-based epoxy has its advantages, there are some key factors to keep in mind:
High VOC Content: Solvent-based epoxy emits volatile organic compounds (VOCs) during application, which can negatively affect indoor air quality and pose environmental concerns. Proper ventilation and safety equipment are essential during installation.
Flammable Properties: The high solvent content makes this type of epoxy flammable during application, increasing the need for caution.
Availability Restrictions: In some states, solvent-based epoxy is banned due to its VOC emissions, limiting its availability in certain areas.
Best Applications for Solvent-Based Epoxy
This type of epoxy is ideal for spaces requiring a durable finish without the higher cost of solid epoxy, such as garages, pedestrian areas, or medium-use commercial spaces.
Water-based Epoxy
Water-based epoxy is the most budget-friendly option available, offering ease of installation and a durable finish for residential use. Made from a blend of water, epoxy, and a hardener, it creates a glossy surface as the water evaporates during curing. Its simple application and environmentally friendly formula make it an appealing choice for homeowners.
Key Benefits of Water-Based Epoxy
Cost-Effective: As the least expensive type of epoxy, it’s perfect for home improvement projects on a budget.
Easy Installation: Installers can apply water-based epoxy without waiting for the concrete substrate to fully dry, saving time during the process.
Low VOCs: This epoxy emits fewer volatile organic compounds, making it a safer and more eco-friendly option for indoor spaces.
Important Considerations
Despite its affordability and ease of use, water-based epoxy has some limitations:
Less Durable: It wears out faster than solid or solvent-based options, leading to more frequent reapplications in high-traffic areas.
Spot Rusting: Over time, water-based epoxy may be prone to rust spots or imperfections.
Limited Applications: This type is not suitable for commercial epoxy flooring or industrial settings due to its reduced resistance to wear and tear and heavy equipment.
Best Applications for Water-Based Epoxy
Water-based epoxy is ideal for light-use spaces such as residential garages, basements, or bathrooms, where heavy traffic and equipment are not a concern..
What Are The Best Rooms for Epoxy Flooring?
Epoxy floors can be the perfect finish for various spaces, but they’re most common in basements, bathrooms, kitchens, patios, and garages.
The table below outlines the costs for these rooms based on average sizes and prices. We used each estimate’s average cost per square foot for epoxy installations.
Your installation may be higher or lower than these estimates based on factors specific to you. We recommend getting a few personalized estimates from professional contractors to ensure the most accurate pricing.
Epoxy flooring offers a wide range of advantages, making it an excellent choice for both residential and commercial spaces. Here’s why it might be the ideal solution for your needs:
1. Enhanced Appearance
Epoxy flooring is a simple yet effective way to add a modern, stylish touch to your home or workspace without requiring a major renovation. Its sleek, clean finish can be customized with features such as:
Multiple colors
Metallic sheens
Decorative elements like stone or quartz flakes
These options allow homeowners to create a look that complements their personal style while elevating the overall aesthetic of the space.
2. Cost-Effectiveness
While repairing cracks or resurfacing concrete may add to the total expense, epoxy flooring is generally more affordable than materials like natural wood or polished concrete. Its straightforward installation process reduces labor costs, making it a budget-friendly investment for both small and large spaces.
3. Exceptional Durability
Epoxy flooring is built to last:
Lifespan: Typically lasts 10 to 20 years in light-traffic areas. With proper care, it can exceed 20 years.
Heavy Use: In high-traffic areas, the lifespan may reduce to 2 to 10 years, but its resistance to abrasion and wear makes it ideal for garages and warehouses. The type of epoxy you select (solid, solvent-based, or water-based) will influence how long your floors last.
4. Eco-Friendliness
Solid and water-based epoxies are low in VOCs, making them safer for indoor air quality and less harmful to the environment. Once cured, epoxy forms a durable, non-contaminating layer, ensuring it doesn’t leach chemicals into the soil or groundwater. However, solvent-based epoxy has a high VOC content, making it less environmentally friendly by comparison.
5. Low Maintenance
Epoxy flooring is easier to maintain than alternatives like natural wood. Simple upkeep includes:
Daily Sweeping: Use a soft-bristled broom to remove dust and debris.
Occasional Mopping: Mop as needed to clean up spills or residual grime. Its non-porous surface makes cleaning quick and hassle-free.
6. Superior Protection
Once dried, epoxy acts as a protective barrier over your existing flooring, shielding it from damage caused by:
Dropped heavy equipment or tools
Oil spills, grease, or chemicals
Everyday wear and tear
This makes it a top choice for garages and workshops, where durability is a priority.
7. Added Safety
Despite its sleek, glossy appearance, epoxy floors are slip-resistant, making them safer for areas exposed to water or spills. Additionally, they are less abrasive than untreated concrete, reducing the risk of scrapes or skin irritation during accidental slips.
DIY vs. Professional Epoxy Flooring Installation
Installing epoxy flooring can be a rewarding DIY project for confident homeowners, but it isn’t always the best approach. Complex installations or issues like cracks, chips, or crumbling concrete substrates often require professional expertise to ensure a flawless, durable finish.
DIY Epoxy Installation
For those looking to save money and take a hands-on approach, DIY epoxy installation can be a viable option. Here’s what to expect:
Epoxy Kits: Affordable and widely available, these kits provide materials and instructions to guide you through the process.
Challenges: DIY installations can be tricky without the right tools or experience. Issues like poor adhesion, uneven application, or improper curing are common pitfalls.
Best for Simple Jobs: Ideal for small spaces like residential garages or basements without significant damage to the concrete substrate.
Professional Epoxy Installation
Hiring a professional contractor is often the better choice, particularly for larger or more complex projects. Here’s why:
Expertise and Equipment: Professionals come equipped with specialized tools and materials, ensuring proper adhesion, even coverage, and a long-lasting finish.
Durability: A professional installation typically results in superior resistance to wear and tear, moisture, and abrasion.
Time Savings: Contractors can complete the job efficiently and avoid costly mistakes.
Costs to Consider
Whether you choose DIY or professional installation, the cost of epoxy flooring varies based on the project scope, materials, and labor:
DIY Costs: Epoxy kits typically cost between $2 and $5 per square foot, but additional expenses for tools and preparation materials can add up.
Professional Installation: Contractors charge $6 to $24 per square foot, depending on factors like epoxy type, room size, and customizations.
How Much Does Epoxy Flooring Cost?
The total cost of your epoxy flooring installation depends on factors such as the type of epoxy, the size of the space, and the extent of prep work required.
While this guide provides a general price range, we recommend obtaining personalized quotes from multiple contractors to find the best option for your needs and budget.
FAQs About Epoxy Flooring Costs and Installation
Garage Epoxy Flooring Costs
Q: How much does an epoxy garage floor cost? A: An epoxy garage floor typically costs between $3 and $12 per square foot, depending on the type of epoxy, site preparation, and any custom finishes. For a standard 2-car garage (400 sq. ft.), prices range from $1,200 to $4,800.
Q: How much does epoxy floor cost in a garage? A: On average, a garage epoxy flooring installation costs $3 to $12 per square foot, but factors like traffic coatings, moisture barriers, and professional labor costs can raise the total.
Q: How much does epoxy garage flooring cost? A: The cost varies by project size, materials, and features. A one-car garage (200 sq. ft.) typically costs between $700 and $2,900, while a three-car garage (700 sq. ft.) can cost between $2,200 and $9,500.
Q: How much does it cost to epoxy a garage floor? A: For a professionally installed epoxy garage floor, expect to pay between $6 and $24 per square foot. DIY kits can reduce costs to $2 to $5 per square foot but require additional tools and extensive site preparation.
Q: What does it cost to epoxy a garage floor? A: The total cost depends on factors like the type of epoxy (e.g., water-based, solvent-based, or metallic epoxy), the condition of the concrete substrate, and whether decorative elements, such as quartz flakes, are added.
General Epoxy Flooring Costs
Q: How much does epoxy flooring cost per square foot? A: The cost of epoxy flooring ranges from $3 to $12 per square foot, depending on the epoxy type, room size, and additional features like pigments, sealants, or traffic coatings.
Q: How much does epoxy flooring cost for a 2-car garage? A: A 2-car garage (approximately 400 sq. ft.) will cost between $1,200 and $4,800, depending on whether it’s DIY or professionally installed, and the type of epoxy system used.
Q: How much does metallic epoxy flooring cost? A: Metallic epoxy flooring is a premium option, with prices ranging from $8 to $16 per square foot, due to its reflective and visually striking finish.
Q: How much does epoxy flooring cost for a basement? A: For a 1,000 sq. ft. basement, epoxy flooring typically costs between $2,800 and $11,500, depending on site preparation, moisture control, and whether custom finishes are included.
Q: How much does it cost to epoxy 1,000 square feet? A: The cost for a 1,000 sq. ft. area ranges from $3,000 to $12,000, depending on the type of epoxy coating and the complexity of the project.
DIY vs. Professional Installation Costs
Q: How much does it cost to DIY an epoxy floor? A: DIY epoxy kits cost between $2 and $5 per square foot. However, additional expenses for tools, protective equipment, and site preparation materials should be considered.
Q: How much does professional epoxy flooring cost? A: Professional installation costs range from $6 to $24 per square foot, depending on the type of epoxy, labor fees, and added features like anti-slip coatings or primer applications.
Epoxy Product Costs
Q: How much does a 5-gallon epoxy floor kit cost? A: A 5-gallon epoxy floor kit typically costs between $250 and $600, depending on its quality, included pigments, and whether it’s designed for residential or industrial use.
Q: Where can I buy epoxy floor coating? A: Epoxy floor coatings are available at home improvement stores, specialty flooring retailers, and online. Some brands offer kits with resin, hardener, and basic tools for DIYers.
Q: How much does a 3D epoxy floor cost? A: A 3D epoxy floor, which involves custom designs, costs between $10 and $20 per square foot, depending on the design complexity and the size of the project.
Durability and Maintenance Questions
Q: Are epoxy floors durable? A: Yes, epoxy floors are highly durable and resistant to abrasion, moisture, and chemical spills. With proper care, they can last between 10 and 20 years in residential spaces and up to a decade in high-traffic commercial areas.
Q: Can epoxy floors be repaired? A: Yes, damaged epoxy floors can be repaired by patching cracks, reapplying coatings, or resurfacing. Costs depend on the severity of the damage, ranging from $5 to $15 per square foot for minor repairs.
Regional Epoxy Flooring Costs
Q: How much does epoxy flooring cost in Australia, India, Pakistan, or the Philippines? A: Costs vary by region due to labor and material prices:
Australia: $40 to $100 AUD per square meter
India: ₹200 to ₹600 per square foot
Pakistan: PKR 300 to PKR 1,000 per square foot
Philippines: ₱500 to ₱1,200 per square meter
Epoxy Flooring Costs and Services in Miami and Fort Lauderdale
Garage Epoxy Flooring Costs
Q: How much does it cost to epoxy a garage floor in Miami or Fort Lauderdale? A: In Miami and Fort Lauderdale, epoxy garage flooring costs between $4 and $14 per square foot, depending on factors such as the type of epoxy (solid epoxy, metallic epoxy, or water-based epoxy) and the site preparation required. For a standard 2-car garage (400 sq. ft.), prices range from $1,600 to $5,600, including labor and materials.
Q: How much does it cost to DIY an epoxy garage floor in Miami? A: DIY kits in Miami can cost $2 to $5 per square foot. However, additional expenses for tools like squeegees, spiked rollers, and protective equipment may increase the total. DIY can save money, but professional installation ensures better durability and adhesion in South Florida’s humid climate.
General Epoxy Flooring Costs
Q: How much does epoxy flooring cost per square foot in Fort Lauderdale? A: In Fort Lauderdale, the average cost for epoxy flooring installation is between $4 and $12 per square foot. For metallic epoxy or high-end custom finishes, costs can rise to $16 per square foot.
Q: How much does epoxy flooring cost for a basement in Miami? A: Epoxy flooring for a typical 1,000 sq. ft. basement in Miami costs between $3,000 and $12,000, depending on whether moisture mitigation is required due to South Florida’s high water table and humidity.
Specific Applications and Features
Q: How much does metallic epoxy flooring cost in Miami and Fort Lauderdale? A: Metallic epoxy flooring costs between $8 and $16 per square foot in Miami and Fort Lauderdale. It’s a premium option ideal for creating luxurious finishes in kitchens, living rooms, and commercial spaces.
Q: How much does it cost to epoxy 1,000 square feet in Fort Lauderdale? A: Epoxy flooring for a 1,000 sq. ft. space costs $4,000 to $12,000, depending on the epoxy type, customizations like quartz flakes, and the level of site preparation needed.
Local Services and Contractors
Q: Who installs epoxy flooring near me in Miami? A: There are several reputable contractors in Miami and Fort Lauderdale specializing in epoxy flooring installation, including companies like Epoxy Miami Flooring and Fort Lauderdale Epoxy Pros. Always request free quotes and compare contractors to ensure you’re getting competitive pricing.
Q: How much does it cost to have a garage floor epoxied in South Florida? A: Professional garage floor epoxy installation costs between $1,600 and $5,600 for a standard 2-car garage in Miami or Fort Lauderdale. Costs may vary depending on the contractor and the inclusion of features like anti-slip coatings or UV-resistant finishes for outdoor garages.
Regional Considerations
Q: Are epoxy floors suitable for Miami’s humid climate? A: Yes, epoxy floors are highly durable and moisture-resistant, making them ideal for Miami’s high humidity. However, proper site preparation is essential to address any existing moisture issues in the concrete slab before application.
Q: How long do epoxy floors last in Miami and Fort Lauderdale? A: With proper installation and maintenance, epoxy flooring in South Florida can last 10 to 15 years in high-traffic areas like garages and 15 to 20 years in residential basements or kitchens.
Product and Cost Questions
Q: Where can I buy epoxy floor coating in Miami or Fort Lauderdale? A: You can purchase epoxy floor coatings at local home improvement stores like Home Depot or Lowe’s, as well as specialty suppliers like South Florida Concrete Coatings. Many retailers also offer complete kits for DIY projects.
Q: How much does a 5-gallon epoxy floor kit cost in South Florida? A: A 5-gallon epoxy kit in Miami or Fort Lauderdale costs between $250 and $600, depending on the quality, pigments, and whether it’s designed for commercial-grade durability or residential use.
Why Choose Epoxy Flooring in Miami and Fort Lauderdale?
Humidity Resistance: Epoxy flooring is ideal for South Florida’s humid climate due to its resistance to moisture and mold growth.
Durability: Epoxy is highly resistant to wear and tear, making it perfect for garages, warehouses, and outdoor patios.
Aesthetic Options: Custom finishes like metallic epoxy, decorative flakes, and pigments allow homeowners to create stunning, unique floors that suit any space.